Recognizing the Trick Components and Fixing Approaches for Product Packaging Equipment Maintenance
Efficient maintenance of product packaging equipments depends upon an extensive understanding of their key elements, consisting of the framework, drive system, and sealing mechanisms. Acknowledging common maintenance problems, paired with the implementation of preventative methods and repairing techniques, can substantially improve equipment reliability. Moreover, the choice of repair practices, consisting of using OEM components and the importance of licensed service technicians, plays a critical role in lessening downtime. To really realize the ins and outs of these systems and their upkeep, one need to take into consideration the broader implications of overlooking these essential methods.
Trick Parts of Packaging Devices
Product packaging machines consist of numerous vital parts that interact to ensure reliable and efficient packaging procedures. At the core of these equipments is the frame, which supplies structural integrity and houses the various operating components. The drive system, frequently a combination of electric motors and gears, assists in the activity of elements, allowing precise operation throughout the packaging cycle.
An additional essential part is the conveyor system, which carries items via different stages of the product packaging procedure. This is often complemented by sensing units and controls that check the setting and rate of items, ensuring synchronization and reducing errors. The loading system is important for precisely dispensing the best quantity of product into plans, whether in fluid, powder, or solid type.
Securing devices, consisting of warmth sealants or glue applicators, play a crucial role in safeguarding packages, avoiding contamination and prolonging rack life. Additionally, labeling systems are essential for offering required item info, making certain conformity with laws. The control panel, geared up with straightforward interfaces, enables drivers to manage machine functions, monitor performance, and make changes as required, ensuring optimal productivity and efficiency in product packaging procedures.
Common Upkeep Concerns
Reliable operation of product packaging devices depends greatly on normal maintenance to protect against usual issues that can interfere with manufacturing. Among these issues, mechanical damage is common, especially in elements like conveyors, seals, and motors, which can result in unforeseen downtimes. Furthermore, imbalance of components can cause inefficient operation, creating items to be incorrectly packaged or damaged throughout the process.
Another common upkeep issue entails the build-up of dirt and debris, which can disrupt the machine's sensors and moving components. packaging machine repair service. This not only impacts efficiency however can also posture safety risks. Lubrication failures can lead to raised friction, resulting in overheating and ultimate component failure.
Electrical issues, commonly stemming from loose links or damaged circuitry, can disrupt machinery features, resulting in considerable manufacturing delays. Software program problems due to improper arrangements or obsolete programs can hinder the machine's operation, necessitating immediate intervention. Resolving these typical maintenance problems proactively is vital for guaranteeing optimal efficiency and durability of packaging machinery.
Preventative Upkeep Methods
Implementing preventative maintenance strategies anchor is critical for sustaining the effectiveness and reliability of packaging machines. These approaches include a methodical technique to upkeep, concentrating on the routine assessment and maintenance of tools to preempt possible failings. By sticking to a set up maintenance program, drivers can determine damage on components prior to they lead to significant malfunctions.
Key components of a preventative upkeep method include regular assessments, component, cleaning, and lubrication substitutes based on supplier referrals. Making use of lists can streamline this procedure, making sure that no crucial jobs are ignored. Furthermore, preserving accurate documents of upkeep tasks aids in tracking the equipment's performance in time, assisting in notified decision-making concerning future upkeep needs.
Training personnel on the relevance of preventative maintenance improves compliance and advice fosters a culture of proactive care. Executing a predictive maintenance part, making use of information analytics and sensor innovation, can further enhance equipment performance by anticipating failures prior to they occur.
Troubleshooting Strategies
When confronted with breakdowns or inadequacies in product packaging makers, using systematic troubleshooting strategies is vital for determining and dealing with issues quickly. The initial step in efficient troubleshooting is to establish a clear understanding of the equipment's functional specifications and efficiency metrics. This entails evaluating the device's specifications, in addition to any type of error notifies or codes presented.
Following, operators should perform an aesthetic evaluation, looking for evident signs of damages, misalignment, or wear. This often includes taking a look at gears, belts, and sensing units to determine prospective root causes of breakdown. Gathering functional data, such as manufacturing prices and downtime logs, can also provide insights right into persisting problems.
Once possible issues are identified, utilizing a logical technique to separate the origin cause is critical. This may need testing individual parts or systems in a controlled fashion. Involving i loved this in conversations with drivers who interact with the machinery on a regular basis can produce beneficial comments regarding unusual habits or patterns.
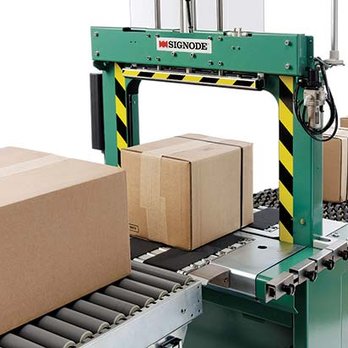
Fixing and Substitute Best Practices
A thorough understanding of repair service and replacement best practices is crucial for keeping the long life and efficiency of packaging equipments. Regularly examining the problem of equipment parts permits prompt intervention, preventing more significant problems that can cause costly downtimes.
When fixings are needed, it is necessary to utilize OEM (Original Equipment Manufacturer) components to make certain compatibility and efficiency. This not just protects the stability of the device however additionally supports guarantee arrangements. Furthermore, it is suggested to maintain an inventory of vital extra components to assist in fast replacements and lessen operational disruptions.
For complex repair services, involving qualified specialists with specialized training in packaging equipment is advised. They possess the expertise to diagnose issues accurately and implement fixings efficiently. Documenting all fixing activities and parts replacements is crucial for keeping a thorough upkeep background, which can help in future troubleshooting.
Last but not least, applying a proactive technique, consisting of routine assessments and anticipating maintenance strategies, boosts the integrity of packaging machines. By sticking to these best practices, companies can make sure ideal equipment performance, decrease operational risks, and expand devices life-span.
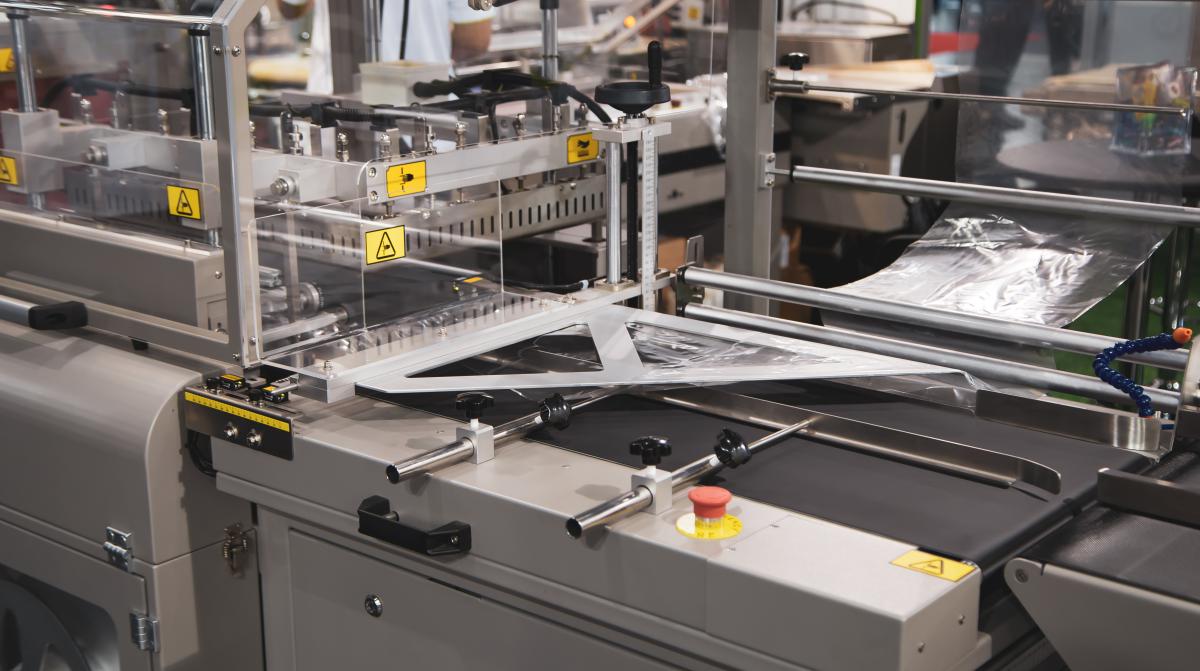
Verdict
Finally, a thorough understanding of packaging maker elements and efficient maintenance methods is important for ideal efficiency. Normal examinations and the use of OEM parts can significantly decrease downtime, while a well-documented maintenance history promotes positive care. Utilizing licensed service technicians better improves repair quality and dependability. By carrying out these practices, organizations can make certain the long life and effectiveness of packaging machines, ultimately adding to improved operational performance and lowered expenses.
Reliable upkeep of product packaging equipments hinges on an extensive understanding of their key elements, consisting of the structure, drive system, and sealing mechanisms.Reliable procedure of packaging machines relies greatly on normal upkeep to avoid common issues that can interfere with manufacturing.Carrying out preventative maintenance methods is vital for sustaining the performance and dependability of product packaging machines. Furthermore, keeping precise records of maintenance activities help in tracking the device's performance over time, facilitating informed decision-making concerning future upkeep needs.
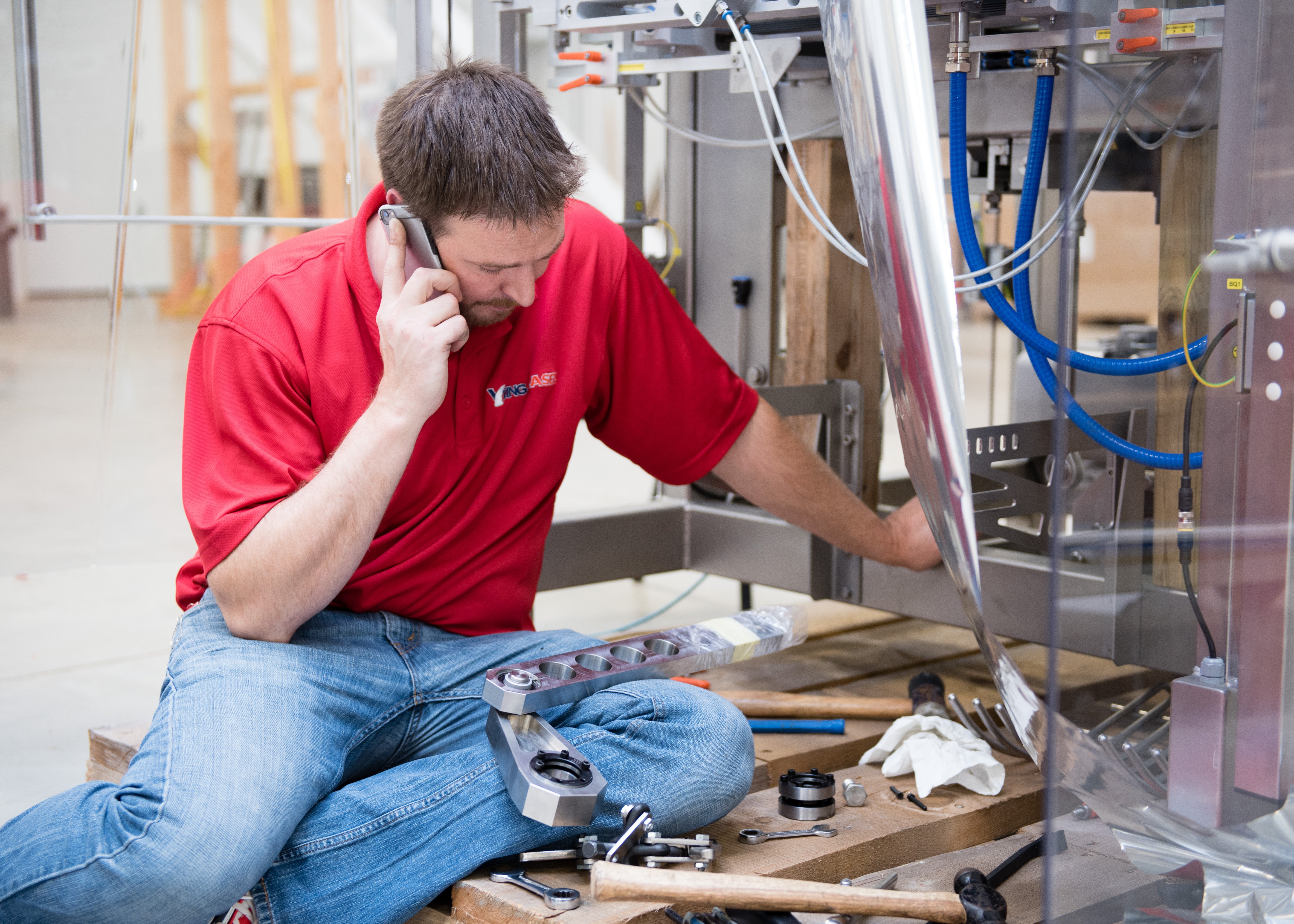